Turbogenerator Diagnostics | Phantom Gen 3
In this case study, a vibration analysis of a turbogenerator is presented, with the objective of identifying possible problems and taking preventive measures to guarantee its optimal operation. The Erbessd Phantom vibration analysis equipment was used, which allows accurate and reliable measurements. Throughout the study, emphasis was placed on the detection of imbalances and misalignments in the turbine and generator rotors, as well as possible clearances in the bearings.
Details Observed in the Unit
Multiple reports were received detailing significant increases in turbogenerator vibration during load operation. This concerning phenomenon became more evident at a specific period of the day, primarily between 5am and 9am. Reports of vibration increases were persistent and the severity of these initial details became a cause of great concern to all involved in the operation and maintenance of the turbogenerator.
Faced with this situation, a strategic decision was made to conduct a thorough and meticulous vibration analysis. The main objective of this analysis was to identify the underlying causes of the vibration increases, in order to thoroughly understand the nature of the problem and develop effective and lasting solutions to address it.
The analysis was conducted with the utmost attention to detail, using advanced vibration measurement and monitoring tools and techniques.
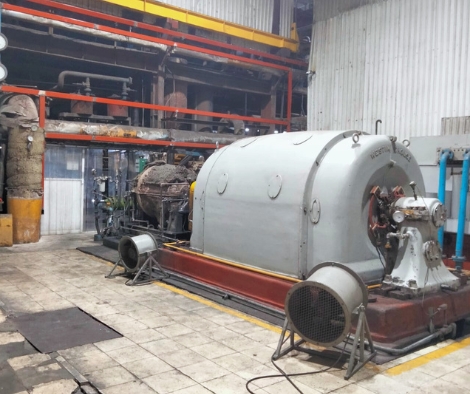
Tasks Performed: Initial Vibration Analysis
To better understand the normal operating conditions and to rule out problems at the time of analysis, an initial vibration analysis was performed using portable equipment. The measurements revealed the presence of residual unbalance in the turbine and generator rotors, as well as misalignment between the two components and possible looseness in the bearings. The vibration spectra in figures 1 to 4 illustrate the behavior of the turbogenerator operating under load at 17:54 hours on Tuesday, February 21.
Based on these results, it was recommended that the turbogenerator be instrumented with wireless triaxial Phantom Gen 3 accelerometers and that a periodic monitoring program be implemented.
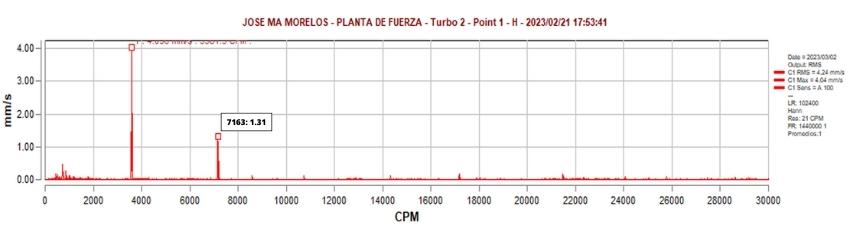
FIG. 1. INITIAL CONDITION VIBRATION SPECTRUM POS1H
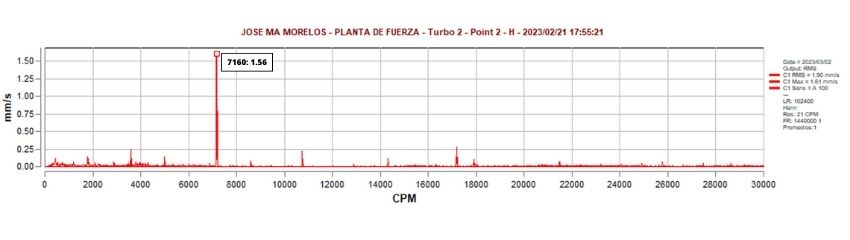
FIG. 2. INITIAL CONDITION VIBRATION SPECTRUM POS2H
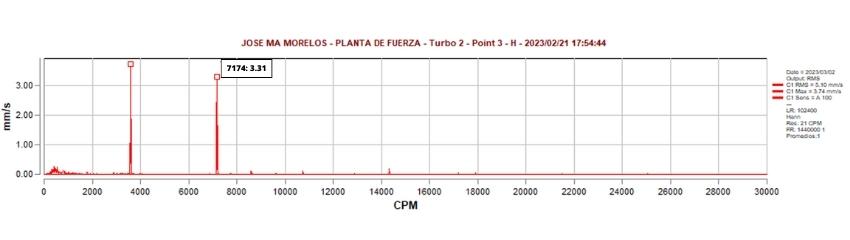
FIG. 3. INITIAL CONDITION VIBRATION SPECTRUM POS3H
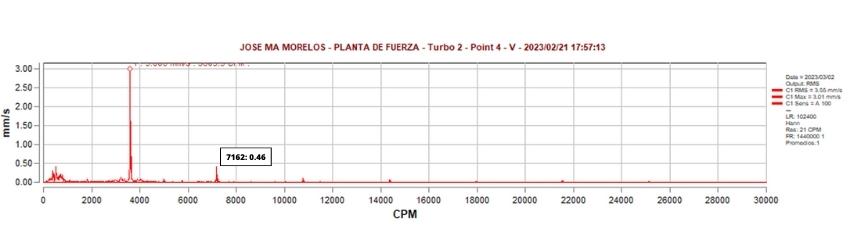
FIG. 4. INITIAL CONDITION VIBRATION SPECTRUM POS4V
Instrumentation for Programmed Measurements
In order to obtain programmed and continuous measurements, a meticulous installation of a set of four low range Phantom Gen 3 wireless triaxial accelerometers was carried out. Each accelerometer was carefully placed in a different bearing, ensuring a balanced and representative distribution of key areas of the turbogenerator. Vibration readings were scheduled to be recorded every half hour, providing constant and detailed monitoring of the dynamic behavior of the equipment.
The monitoring system was accurately and reliably commissioned at 19:18 hours on February 21. From that point on, the accelerometers began capturing and recording vital vibration data in real time. This process continued uninterrupted until March 10, covering a substantial period that allowed for a comprehensive analysis of vibration and temperature patterns and variations over time.
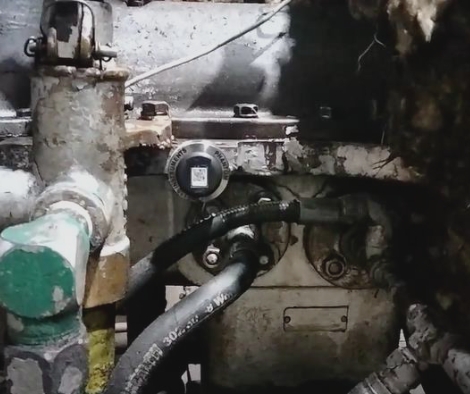
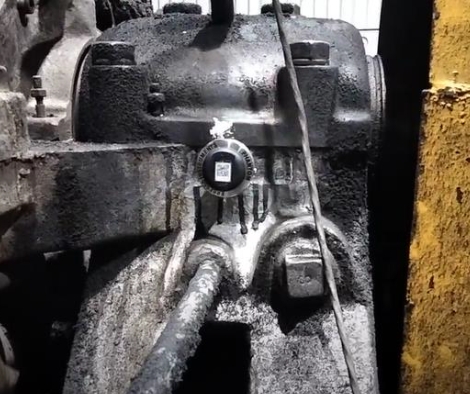
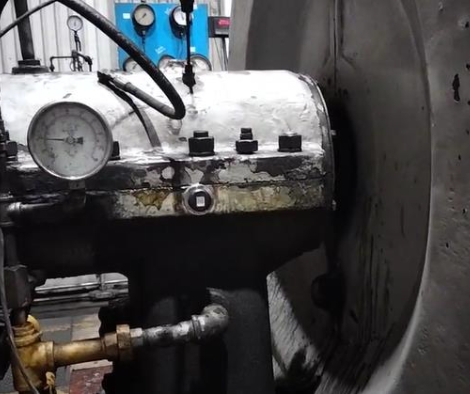
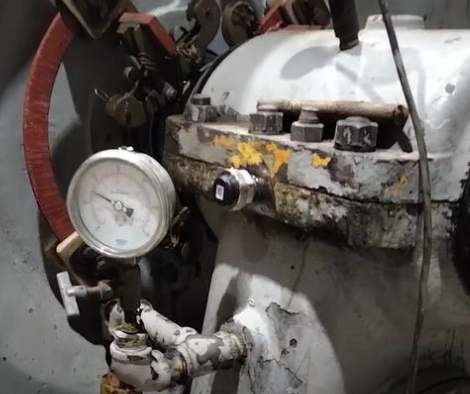
During monitoring, vibration levels were recorded at each measurement point in the horizontal, vertical and axial directions, as well as temperature readings at each bearing. A significant change was observed at bearing 3 (generator coupling side) in the vertical direction, with an increase in vibration during nighttime measurements when the ambient temperature was lower.
To analyze the important events in detail, the overall vibration trend plots and their relationship to bearing temperature are presented. These plots provide information on the three most relevant events during the measurements.
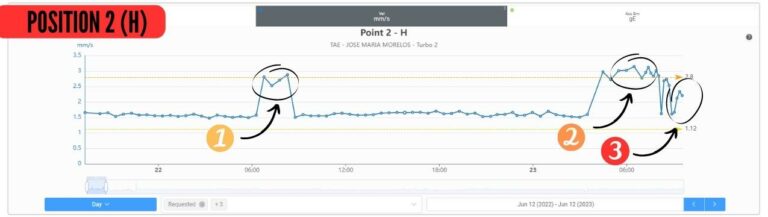
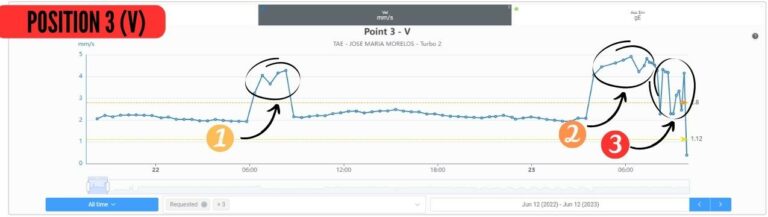
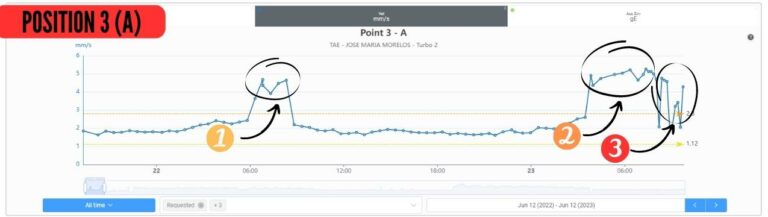
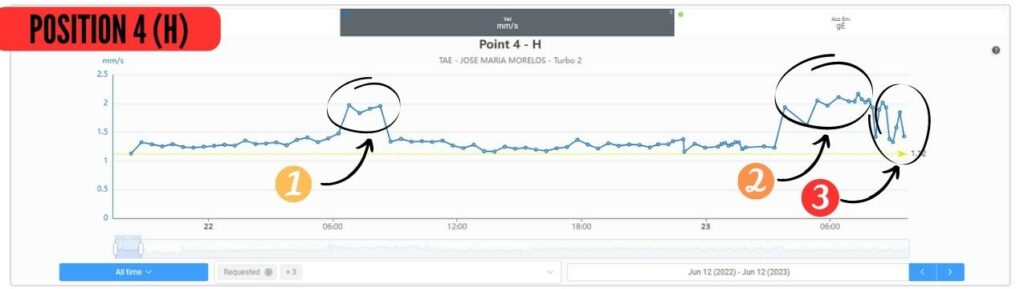
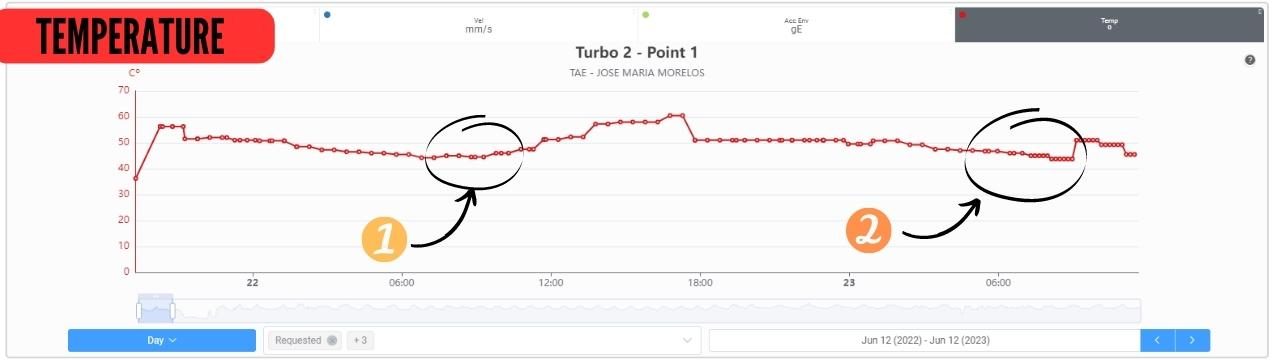
Critical Events
EVENT 1
Start: February 22, 06:30 hours
End: February 22, 08:30 hours
Thanks to the Phantom 3G sensors installed in the turbogenerator, vibration signals were captured at the four monitored points in all directions (H, V, A). A significant increase in vibration was observed at positions 2 and 3 (coupling side turbine bearing and coupling side generator bearing). By analyzing the vibration spectra, it was determined that this increase was due to changes in lubrication oil temperature, generating the condition of oil whirl in both bearings.
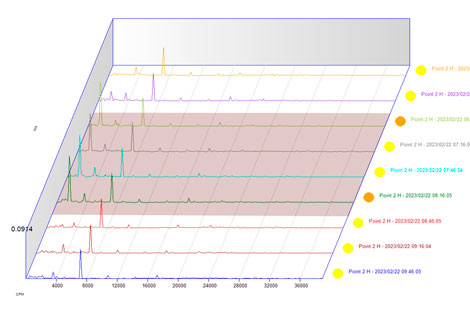
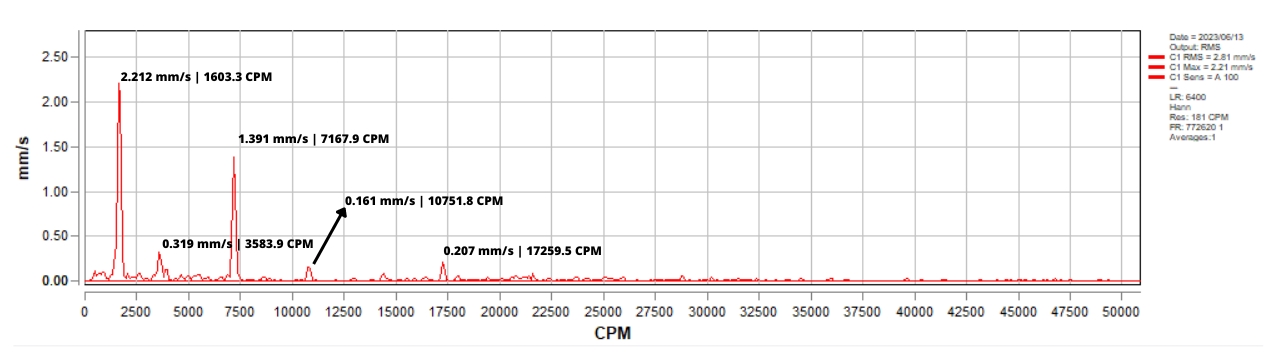
EVENT 2
Start: February 23, 03:50 hours
End: February 23, 08:00 hours
In accordance with the ambient temperature conditions, it was found that event 2 occurred prior to event 1. The second measurement reaffirmed the correlation between the oil temperature variation and the occurrence of the phenomenon known as oil whirl. It is pertinent to highlight the presentation of the cascade spectra corresponding to positions 2 and 3, which undeniably show the extremely important changes.
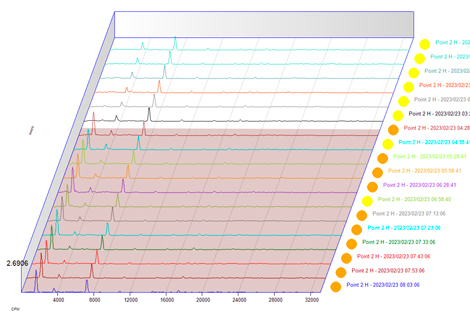
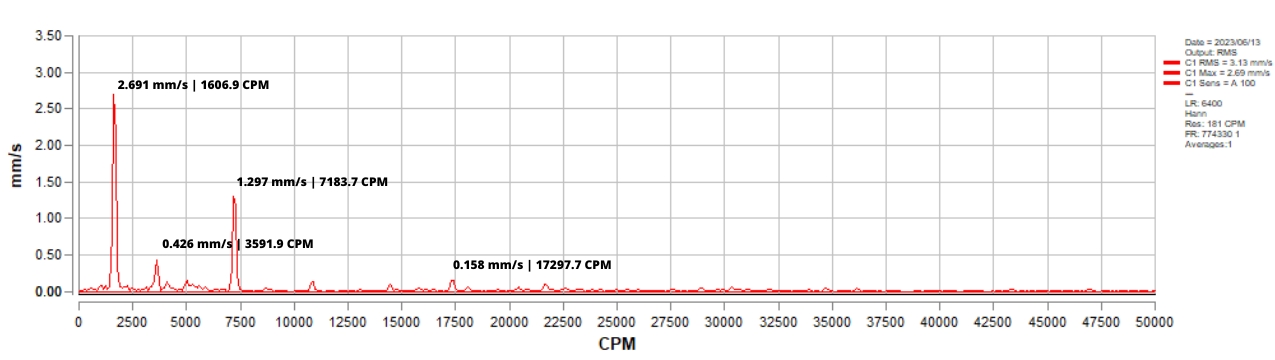
EVENT 3
Start: February 23, 07:50 hours
End: February 23, 09:24 hours
To confirm the effect of oil temperature on the oil whirl condition, a test (EVENT 3) was performed by manually modifying the oil temperature by restricting the cooling water flow in the oil cooler. It was observed that the oil whirl disappeared completely when the temperature was modified, evidencing its close connection with this phenomenon. This temperature modification was carried out on two occasions, and it was clearly observed that the oil whirl condition disappeared completely.
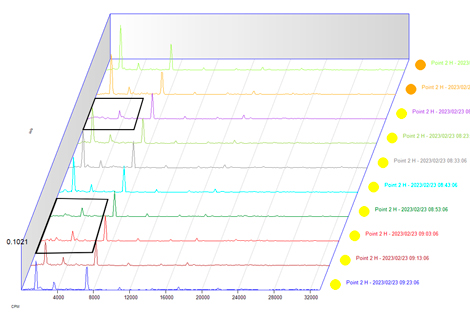
Diagnosis
The obtained results highlight the close relationship between the oil whip phenomenon and temperature variations. Through two controlled temperature modifications, the complete disappearance of oil whirl could be observed in a conclusive manner.
These findings are of utmost importance because they demonstrate that oil whip is directly influenced by the temperature of the system. By modifying the temperature, this undesirable phenomenon is completely suppressed.
Subsequent Analysis and Results After Corrections
In the new analysis performed on February 25, normal operation of the turbogenerator was observed while operating under load. A vibration analysis was performed at a distance between the turbine and the generator to evaluate its performance.
The results of the analysis indicated that the vibration levels were within the range of acceptability in both the steam turbine and generator rotor, with the presence of 1XT order components due to residual unbalance in the turbine and generator rotors.
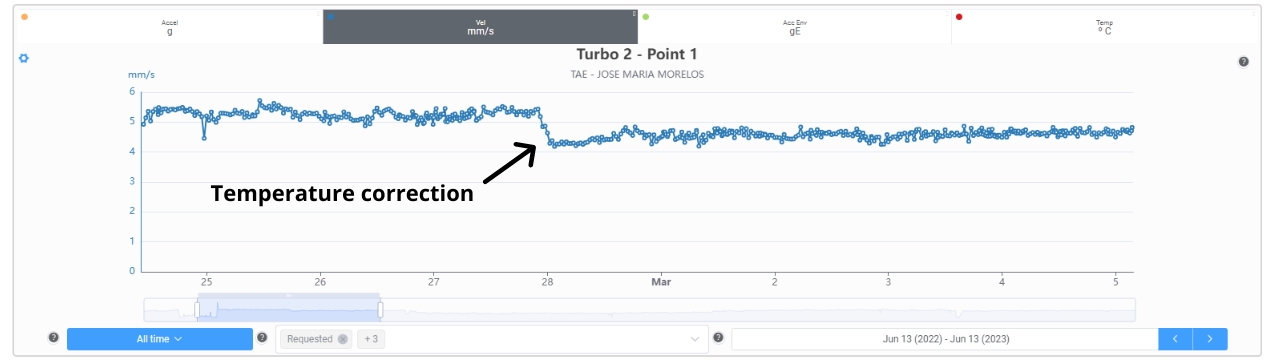
As part of the recommendations based on these results, it is suggested to evaluate the possibility of installing an oil temperature control system that allows maintaining variations no greater than 7°C. In addition, it is recommended to review the geometries and gaps of the bearings in future opportunities, taking advantage of the experience of the plant personnel, with the objective of eliminating any oil leakage from the trunnion bearing system.
In case of experiencing a 30% increase in vibrations due to unbalance, it is recommended to schedule a balancing of the turbine and generator rotors. This balancing can be performed on site with a portable balancing machine or by sending the rotors to a specialized balancing shop.
The turbogenerator will continue to be monitored until Friday, March 10, in order to detect any significant changes in its behavior. If any anomaly is found during this period, it will be reported in a timely manner.
In conclusion, the vibration analysis performed with the help of the Phantom sensors has allowed to diagnose and understand the problems of increased vibration in the turbogenerator. Through programmed monitoring and recording of vibration signals at different points, residual unbalance, misalignment and the presence of oil whip were identified as the main causes of abnormal vibrations.
In addition, thanks to the Phantom sensors, indirect temperature readings of the lubrication oil were obtained during operation, which proved crucial in relating temperature changes to the occurrence of oil whip. This accurate diagnosis provides a solid basis for implementing recommendations and taking the necessary corrective actions, ensuring optimal and safe operation of the turbogenerator.
Vibration analysis using advanced technologies, such as Phantom sensors, proves its value in the field of predictive maintenance and monitoring of rotating equipment. By providing accurate, real-time data on the dynamic behavior of equipment, major damage and costly unplanned shutdowns can be avoided, thus ensuring the efficiency and reliability of industrial facilities.
With more than 50 years of experience in vibration analysis, TAE Vibraciones has specialized in the sugar mill sector, having provided services in more than 30 locations throughout the country.
TAE Vibraciones‘ chief engineer, Oscar Yrigoyen Lazeri, leads the team with his extensive knowledge and experience in the field. In addition to their vibration analysis services, TAE Vibraciones is an official distributor of Erbessd Instruments. This allows them to represent and offer this state-of-the-art equipment throughout Mexico.
If you would like to learn more about the services provided by TAE Vibraciones, establish contact or sales requirements, please do not hesitate to contact us at the following e-mail address:
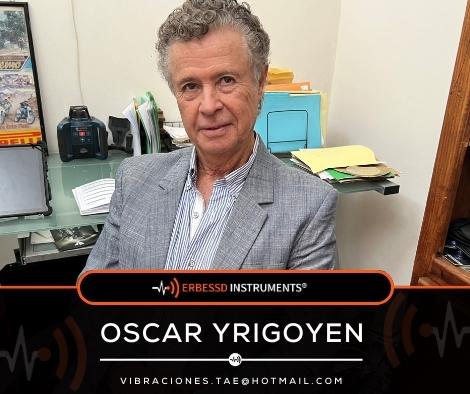