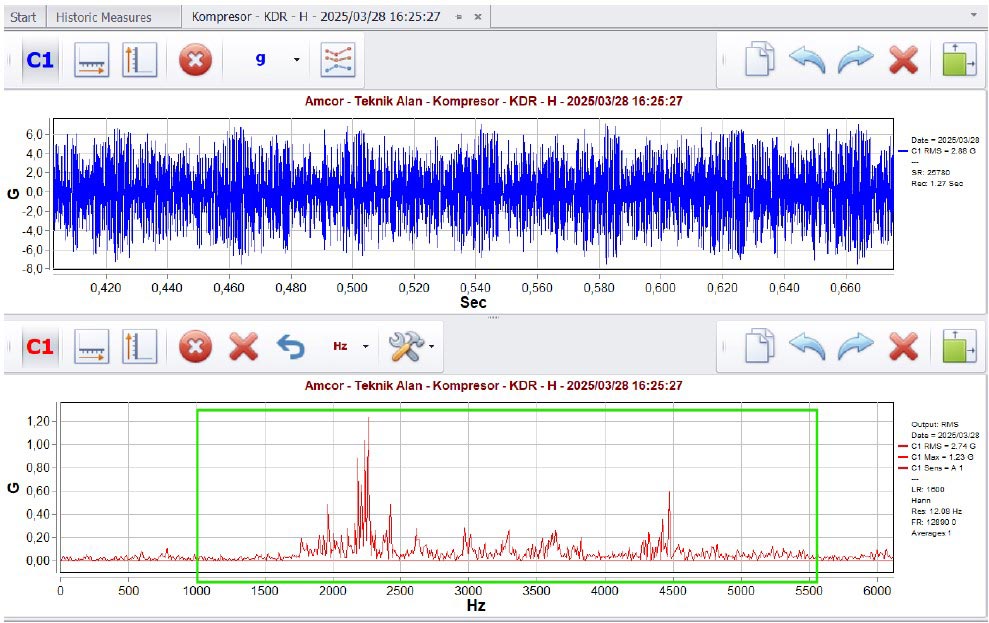
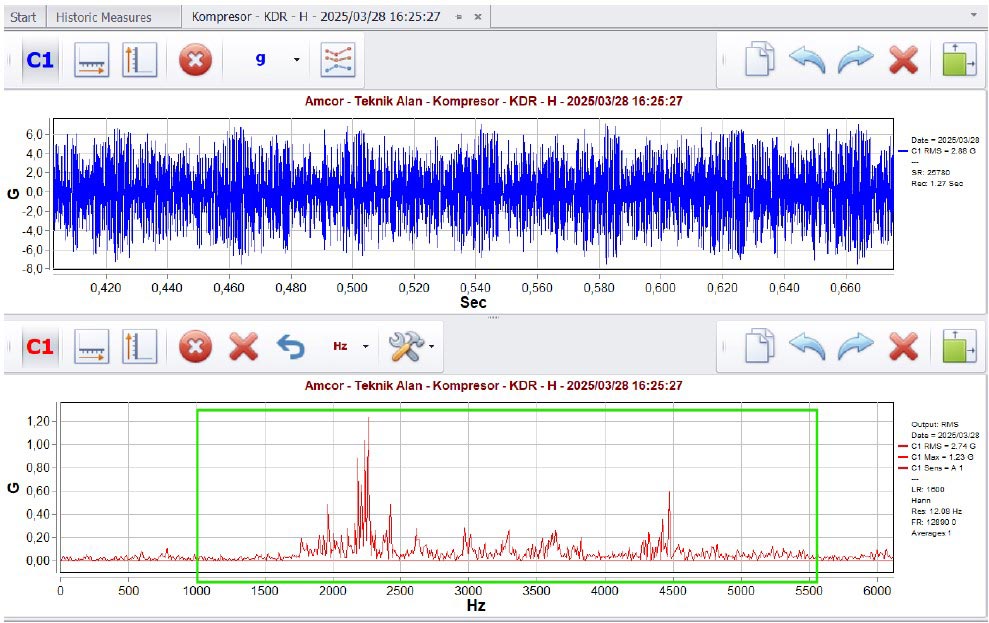
A collaboration between Erbessd Instruments and Regnus Engineering Solutions.
At Erbessd Instruments, we believe success starts with early detection. This success story highlights how our technology, in partnership with Regnus Engineering, helped Amcor Flexibles prevent failures, reduce risk, and build confidence in proactive maintenance practices — even on newly installed machinery.
Amcor Flexibles – Packaging Material Coating Facility.
Location: Gebze, Turkey.
Partner: Regnus Engineering Solutions.
Date: March 25, 2025.
Project Lead: Eray Engin, ISO-CAT-2 Certified.
Amcor Flexibles raised concerns about unusual noise from a new air compressor only two months into operation.
While the manufacturer attributed it to a lack of lubrication, Amcor requested a second opinion from Regnus Engineering to validate the root cause and avoid potential costs during the warranty period.
Regnus emphasized that early-stage mechanical issues can affect even brand-new machinery, citing potential mounting, alignment, and manufacturing faults.
Using the ‘Bathtub Curve’ model, they recommended proactive condition monitoring to catch failures early.
– Compressor Power: 110 kW.
– Speed: 1470 RPM.
– Operation: Variable Speed.
– Sensors: Phantom Gen-3 at four points.
– Communication: Gateway-2, Ruth241, EI-Analytic.
– Total Installation Time: 20 minutes.
– Monitoring Period: March 25 – April 10, 3x/day.
Motor Non-Drive End:
– Vibration: 2.80 mm/s (below ISO limit)
– Mechanical looseness and waveform distortion observed.
– Low lubrication suggested by ground noise.
Motor Drive End:
– Vibration: 1.40 mm/s (within safe range)
– Looseness and dry bearing indicators noted
Compressor Drive End:
– Acceleration: 3.81 g (alarm threshold)
– Stage 2 bearing failure indicators
– Bearing replacement recommended under warranty
Compressor Non-Drive End:
– Acceleration: 2.4 g (under alarm limit)
– Stage 1 bearing failure indicators
– Warranty action recommended
– Replace front and rear compressor bearings.
– Fix looseness in motor bearings.
– Lubricate to eliminate ground noise.
– Amcor saw clear benefits from Phantom and EI-Analytic solutions.
– Prevented repair costs and service disruptions.
– Customer plans budget for full project next year.
– Moving toward hybrid service for high-criticality assets.
Want to see how early diagnostics can protect your equipment investment?
Let’s talk about a solution tailored to your operations.
www.erbessd-instruments.com | [email protected]
Regnus Engineering Solutions specializes in delivering innovative industrial services, including predictive maintenance, precision 3D scanning, reverse engineering, and the development of customized spare parts. By combining advanced technology with engineering expertise, the company helps clients optimize operations, reduce downtime, and enhance the longevity and performance of critical machinery and equipment.
ERBESSD INSTRUMENTS® is a leading manufacturer of Vibration Analysis Equipment, Dynamic Balancing Machines, and Condition Monitoring with facilities in Mexico, the USA, England, and India.
Authored by: Eray Engin, Regnus Engineering Solutions
Efforcez-vous de vous améliorer et de viser la qualité.
Depuis les États-Unis. +1 (518) 874 2700
Du Mexique (55) 6280 7654 | (99) 9469 1603
dans le monde entier +1 (877) 223 4606
Ou CONTACTEZ-NOUS