
Maximizing ROI with Proactive Condition Monitoring: A Cost-Driven Analysis of the Goulds 11AI1U9A0 Centrifugal Pump
1. Introduction: From Cost Center to Competitive Advantage
Industrial assets like the Goulds 11AI1U9A0 centrifugal pump are critical in high-demand environments such as pulp and paper manufacturing. However, the total cost of ownership (TCO) extends far beyond the sticker price. Traditional preventive maintenance practices often lead to unforeseen downtime and costly emergency interventions. Modern manufacturing, however, demands data-driven reliability. By integrating condition monitoring (CM) and predictive analytics, facilities can transform reactive maintenance into a strategic, ROI-positive initiative.
2. Investment Snapshot: Goulds 11AI1U9A0 Centrifugal Pump
Base Pump Cost: $25,000 – $40,000
Installation & Commissioning: $5,000 – $10,000
Total Initial Investment: $30,000 – $50,000
Without enhanced monitoring, the expected lifespan is 7–10 years, depreciating roughly 10% annually. But this figure shifts dramatically with smart analytics in play.
Total Cost of Ownership (TCO): Maintenance expenses can constitute around 20% of a pump’s total cost of ownership. Given that initial purchase costs often represent less than 10% of TCO, this highlights the significance of maintenance in the overall financial picture (RF MacDonald Co., 2022).
3. The Cost of Conventional Maintenance
Annual Maintenance: $3,500 – $5,000
Emergency Repair Cost: $12,000 – $20,000
Downtime Duration: 3–5 days
Daily Revenue Loss: $41,000 (based on a pulp and paper facility with $15 million in annual sales)
Total Downtime Cost: $205,000
Emergency downtime incurs massive losses. According to Ståhl et al. (2023), the cost behavior of downtimes is dynamic and compounding—small inefficiencies spiral into massive production disruptions if undetected. Real-world operations confirm this scale of impact; a major North American pulp and paper mill reported annual revenues of over $15 million, which aligns with the assumed downtime cost model used in this analysis (2024 Annual Report, IP, p. 9).
4. Reactive Labor Costs Add Up
A maintenance team in reactive mode isn’t just inefficient—it’s expensive
Maintenance Supervisor Salary: $75,000 – $90,000
Reactive Response: $5,000 – $15,000
Total Reactive Maintenance Cost: $80,000 – $105,000
5. Enter Proactive Condition Monitoring
By implementing Erbessd Instruments’ Phantom wireless sensors, DigiVibe, and EI Analytic software, maintenance becomes a predictive, real-time process.
Phantom Sensors: $2,000 – $3,500
DigiVibe + EI Analytic Software: $1,295 – $4,000
Annual Monitoring: $1,200
Total Investment: $4,495 – $7,500
These tools enable early failure detection, trend tracking, and real-time diagnostics. Geary & Cosgrove (2023) highlight how analytics reduce machine downtime by up to 30% while increasing reliability.
6. ROI: Condition Monitoring Pays for Itself
Extended Lifespan: 12–15 years
Avoided Emergency Repair: $12,000 – $20,000
Avoided Downtime: $205,000
Annual Maintenance Savings: $2,000 – $4,000
Reduced Overhead: $5,000 – $10,000
7. Conclusion: Data-Driven Reliability Is the New Standard
Incorporating condition monitoring technology is no longer optional—it’s a strategic imperative. The data clearly shows:
– Emergency downtime is financially devastating.
– Predictive analytics extend equipment life and slash costs.
– The ROI on condition monitoring is achieved within one major incident’s worth of savings.
🔹 Optimize, don’t just maintain. Make your assets work smarter with Erbessd Instruments and redefine reliability in your operation.
Megh Howard serves as the Chief Marketing Officer and Director of People & Culture at Erbessd Instruments. This unique combination allows her to unite the company’s outward-facing brand strategy with its internal culture and values—ensuring that how the company shows up for its customers is deeply rooted in how it operates from within.
Megh believes that a strong, people-centered culture is essential to delivering exceptional customer experiences. By fostering an environment where employees feel valued, connected, and empowered, she helps ensure that customer-first values aren’t just part of the marketing message—they’re lived every day across the organization. Her work aligns employee engagement with service excellence, bridging global teams and creating a workplace that mirrors the trust and support Erbessd Instruments extends to its clients and partners.
A graduate of Hudson Valley Community College and Penn State University, Megh brings a thoughtful, relationship-driven approach to leadership—connecting with colleagues, customers, distributors, and industry peers with authenticity and purpose.
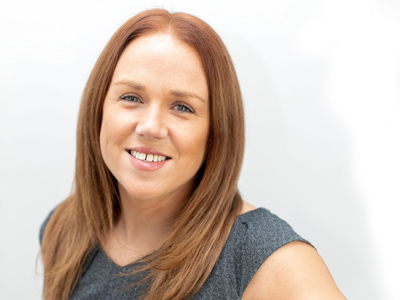