Case Study: Fluted Bearing Detection on a DC Motor Using Erbessd Phantom Sensors and RPM Trigger
This case study documents the detection of a fluted bearing on a DC motor operating under inconsistent speed conditions. Due to fluctuating RPMs
caused by process dynamics and load variability….. With RPM fluctuating between 200–800 RPM, time-based vibration data produced false alarms and
unreliable severity assessments
Solution
Erbessd Phantom wireless sensors are configured to collect data based on specific machine conditions, not just time intervals.
By integrating the Phantom RPM sensor – This approach ensures that vibration data is captured at the right time and under consistent machine conditions,
making trending far more reliable and repeatable

EPH-S40 | Wireless Speed Sensor
This Wireless Speed Sensor uses a Hall effect switch and a
neodymium magnet, all included in the kit. As a result, you can easily
analyze the revolutions per minute of any rotor, turbine or vent with
incredible precision
Wireless RPM Sensor-triggered Phantom Sensors –
synchronized, repeatable, reliable
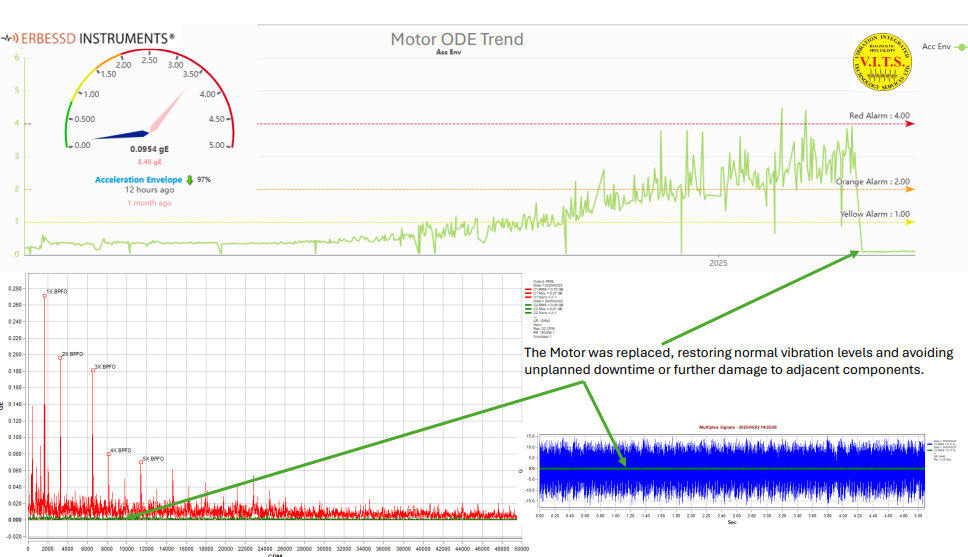
Early Email Alerts from EI Analytics Months before failure,—giving ample time to plan a smooth, stress-free motor change-out.
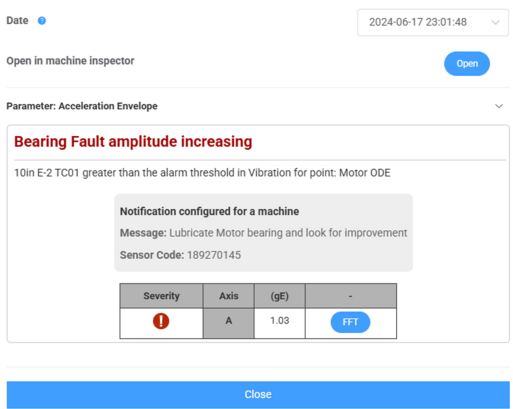
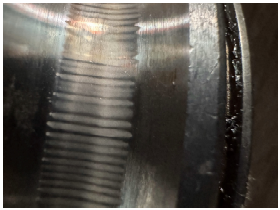
Conclusion
This case study highlights the importance of advanced vibration analysis methods in fluctuating speed machinery like DC motors.
The use of Erbessd Phantom wireless sensors combined with RPM-triggered data acquisition enabled reliable early detection of an issue in a critical bearing.
This case reinforces the need for synchronized diagnostic tools in challenging operating environments